3D PRINTER EXTRUDER
2021 | Client: Electronic Alchemy
Team: Corey Mack, Product Design Engineer | Ben Parnas, Electrical Engineering & PCB Design
PROJECT DESCRIPTION
The 3D Printer Extruder was developed as part of a multi-material 3D printing system, addressing a client requirement for a fanless cooling solution. This unibody extruder utilizes integrated fins to achieve passive cooling, maintaining efficient thermal management without the need for active cooling systems. Designed with a custom PCB to manage sensors, heating elements, and pre-heating capabilities, the extruder is a key component in delivering a versatile, multi-material printing experience.
DESIGN & ENGINEERING
• Fanless, Unibody Design: The extruder’s unibody construction, CNC machined from solid aluminum, integrates cooling fins directly into the design. This solution replaced an earlier approach of using off-the-shelf heatsink fins, which was abandoned due to complexity and cost. The new design provides efficient heat dissipation while reducing production complexity.
• Y-Shaped Structure: The unique Y-shape design of the extruder ensures full constraint against translation and rotation, maintaining stability during operation. This structure also aids in precise positioning within the pick-and-place system, making it easier to manage during material changes.
• Custom PCB: Designed by Ben at BugBeest, the PCB controls power delivery to the onboard sensors and heating elements. This design enables real-time temperature control and pre-heating functionality, making the extruder more adaptable to the diverse needs of multi-material 3D printing.
• Y-Shaped Structure: The unique Y-shape design of the extruder ensures full constraint against translation and rotation, maintaining stability during operation. This structure also aids in precise positioning within the pick-and-place system, making it easier to manage during material changes.
• Custom PCB: Designed by Ben at BugBeest, the PCB controls power delivery to the onboard sensors and heating elements. This design enables real-time temperature control and pre-heating functionality, making the extruder more adaptable to the diverse needs of multi-material 3D printing.
MANUFACTURING STRATEGY
• Low-Volume Production: For prototyping and small-scale production, the extruder is CNC machined from a solid block of aluminum, ensuring high precision and quality.
• Scalable Manufacturing: For larger-scale production, the extruder’s core shape is extruded through a die and then refined with CNC milling to achieve the final form. This approach minimizes material waste and machining time, making the design cost-effective for mass production.
• Modular Design for Flexibility: The extruder is designed for easy attachment and detachment from the pick-and-place machine using a motorized screw mechanism. When not in use, the extruders are stored on a wall-mounted rack, where magnets and the Y-shaped design ensure secure placement.
• Scalable Manufacturing: For larger-scale production, the extruder’s core shape is extruded through a die and then refined with CNC milling to achieve the final form. This approach minimizes material waste and machining time, making the design cost-effective for mass production.
• Modular Design for Flexibility: The extruder is designed for easy attachment and detachment from the pick-and-place machine using a motorized screw mechanism. When not in use, the extruders are stored on a wall-mounted rack, where magnets and the Y-shaped design ensure secure placement.
INNOVATIVE POWER MANAGEMENT
• Reduced Wiring Complexity: The extruder receives power directly from the pick-and-place machine or wall-mounted rack, significantly reducing the need for long wiring harnesses. This strategy minimizes potential failure points and allows the extruder to preheat while stationed on the wall, improving workflow efficiency.
• Spring-Loaded Pin Connections: Power is conveyed through spring-loaded pins, a safer alternative to the original stationary pin design, which posed a spark hazard. This solution provides a reliable and safe power connection while reducing the risks of fire or electrical faults.
• Spring-Loaded Pin Connections: Power is conveyed through spring-loaded pins, a safer alternative to the original stationary pin design, which posed a spark hazard. This solution provides a reliable and safe power connection while reducing the risks of fire or electrical faults.
USER EXPERIENCE & AESTHETICS
• Anodized Finish: Each extruder can be anodized in different colors, such as gold, allowing for easy identification of extruders dedicated to specific materials. This not only enhances the visual appeal but also simplifies the management of multi-material setups.
• Compact Form Factor: The extruder’s sleek design fits seamlessly into the 3D printer setup, reducing clutter and making it easier for users to swap out extruders as needed. The fanless design ensures quieter operation, contributing to a more user-friendly and professional printing environment.
• Compact Form Factor: The extruder’s sleek design fits seamlessly into the 3D printer setup, reducing clutter and making it easier for users to swap out extruders as needed. The fanless design ensures quieter operation, contributing to a more user-friendly and professional printing environment.
Why This Matters
The 3D Printer Extruder project showcases my ability to meet complex client requirements through innovative design and engineering. By developing a fanless cooling solution that is both cost-effective and scalable, I was able to create a product that meets the diverse needs of multi-material 3D printing. The design balances technical complexity with user-friendly features, such as simplified power management and intuitive attachment mechanisms, making it suitable for both prototype and high-volume production. This project demonstrates my commitment to delivering solutions that are as practical as they are cutting-edge, aligning technical advancements with real-world user needs.
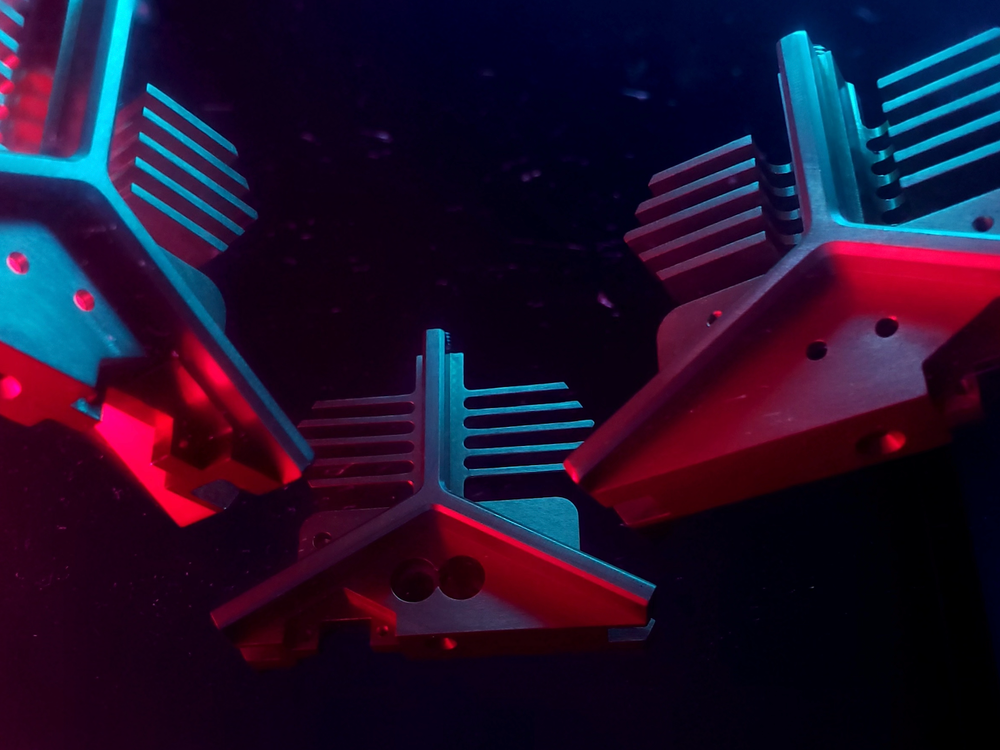
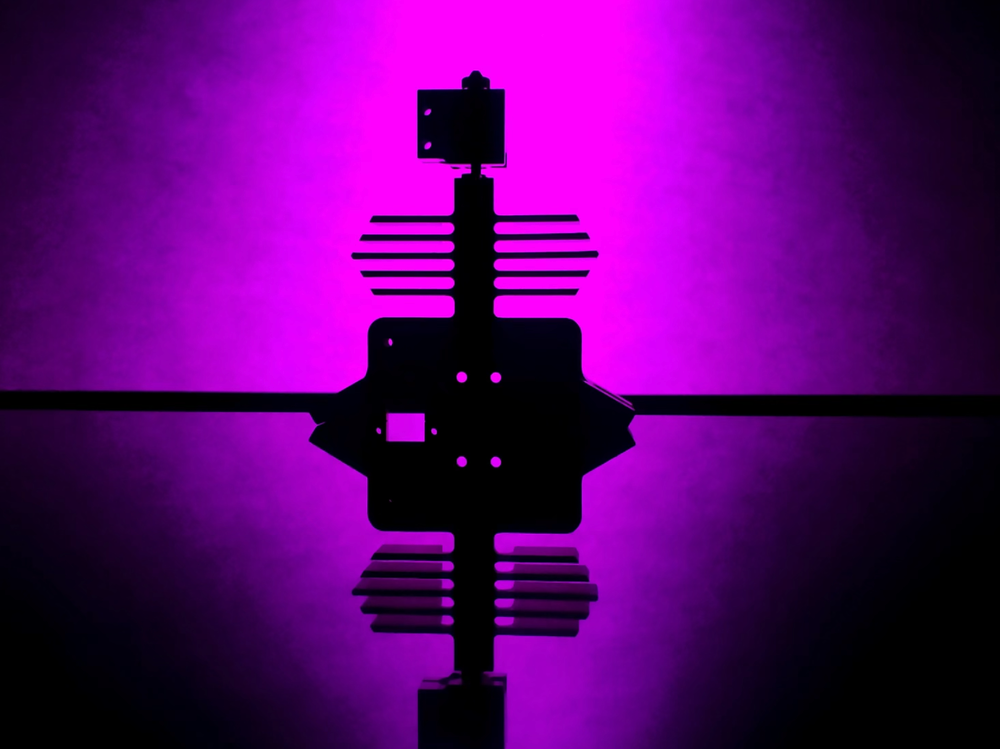
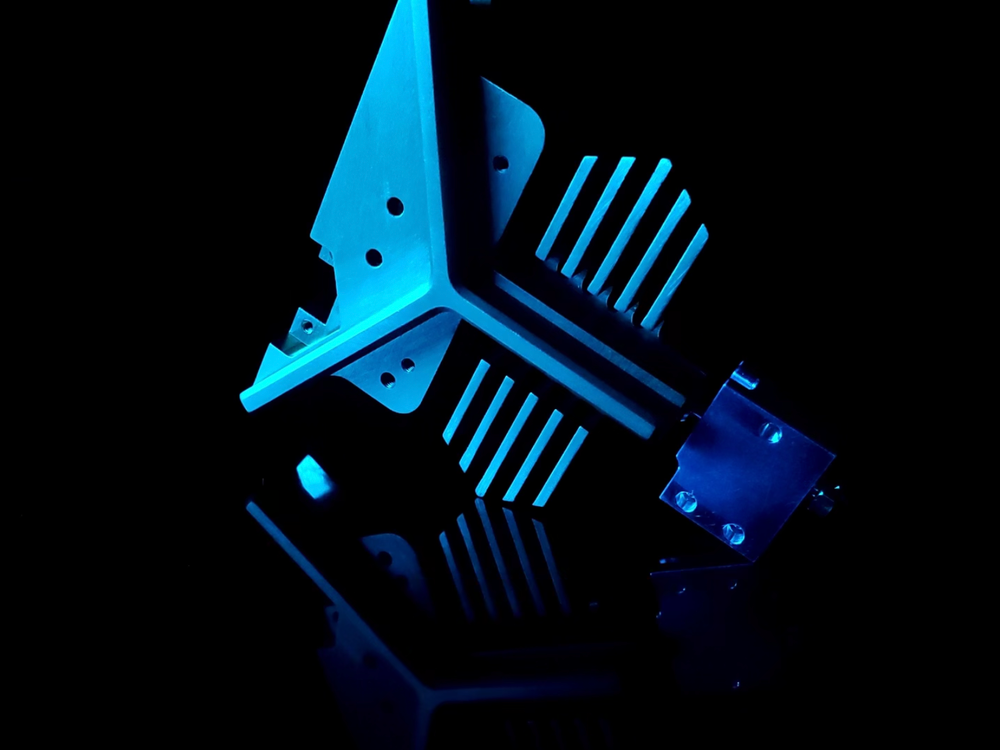
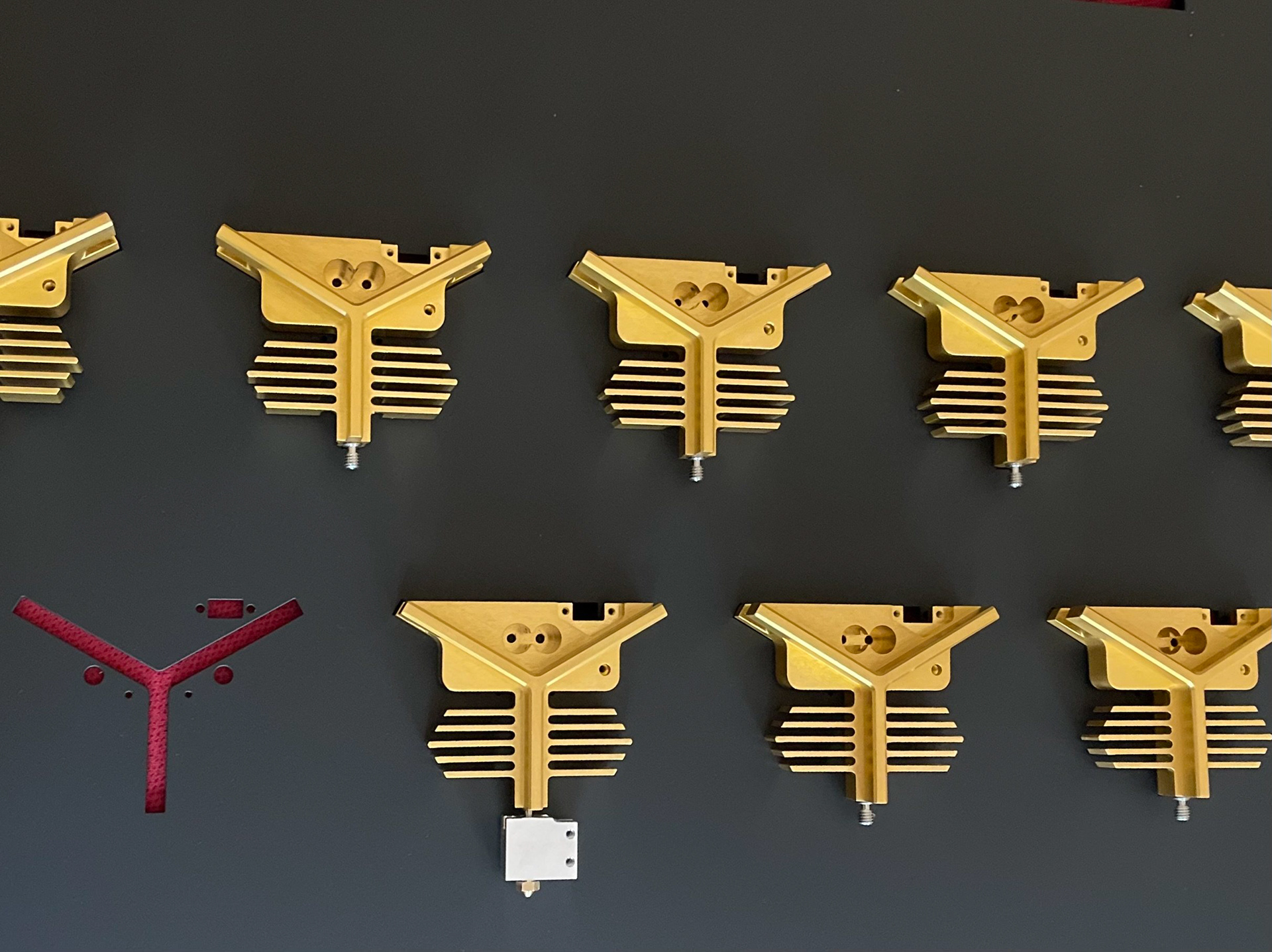
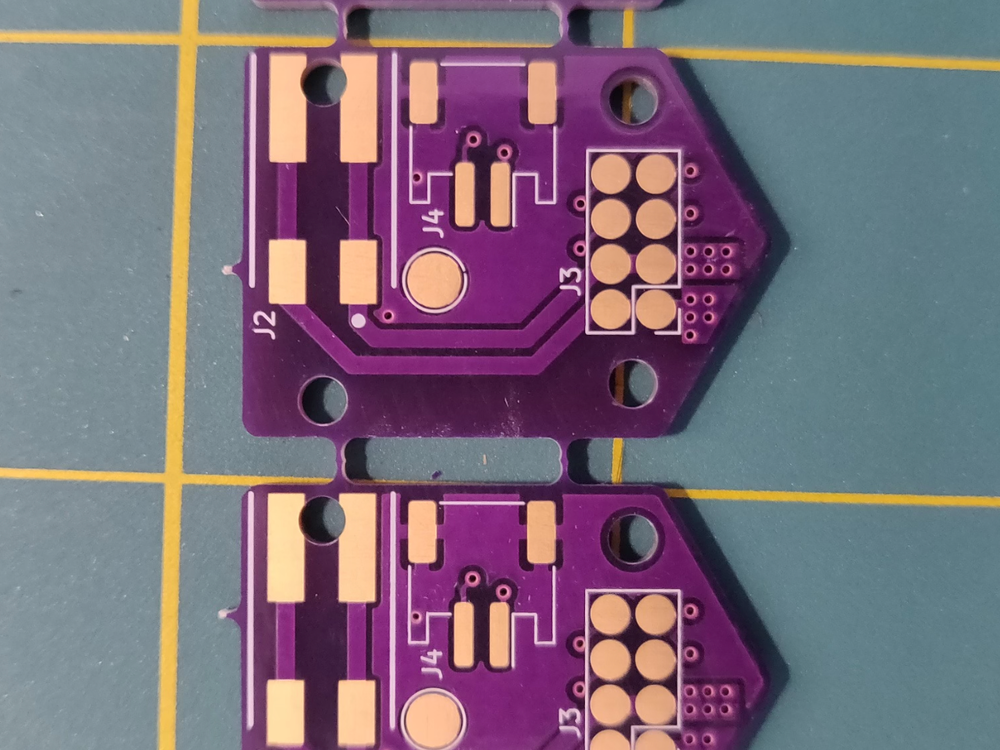
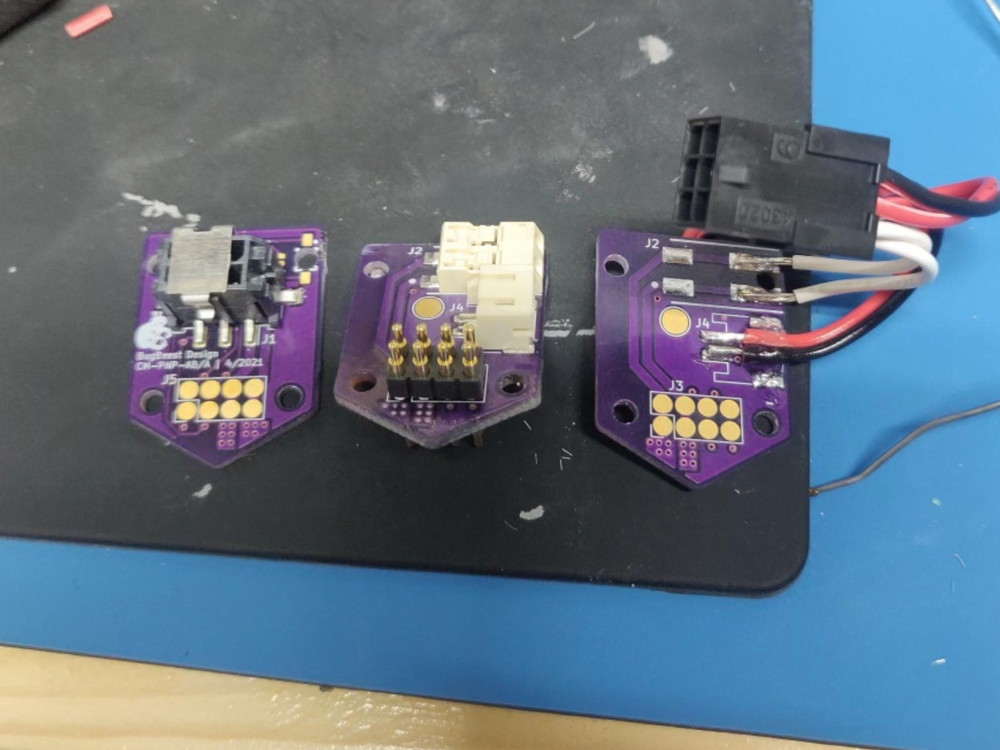
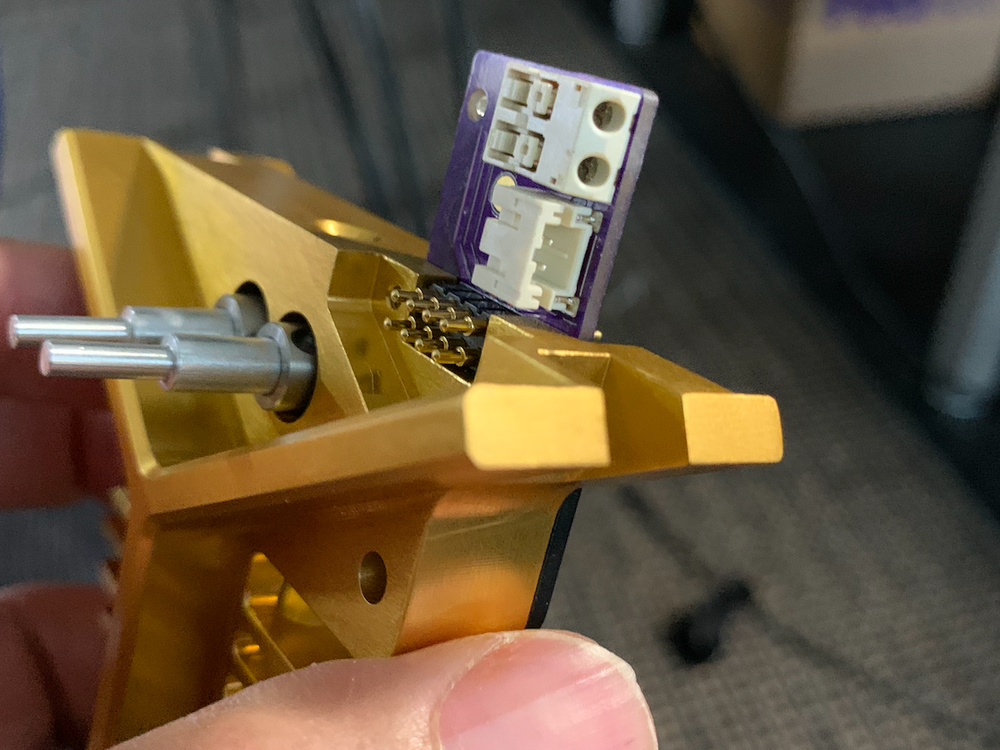
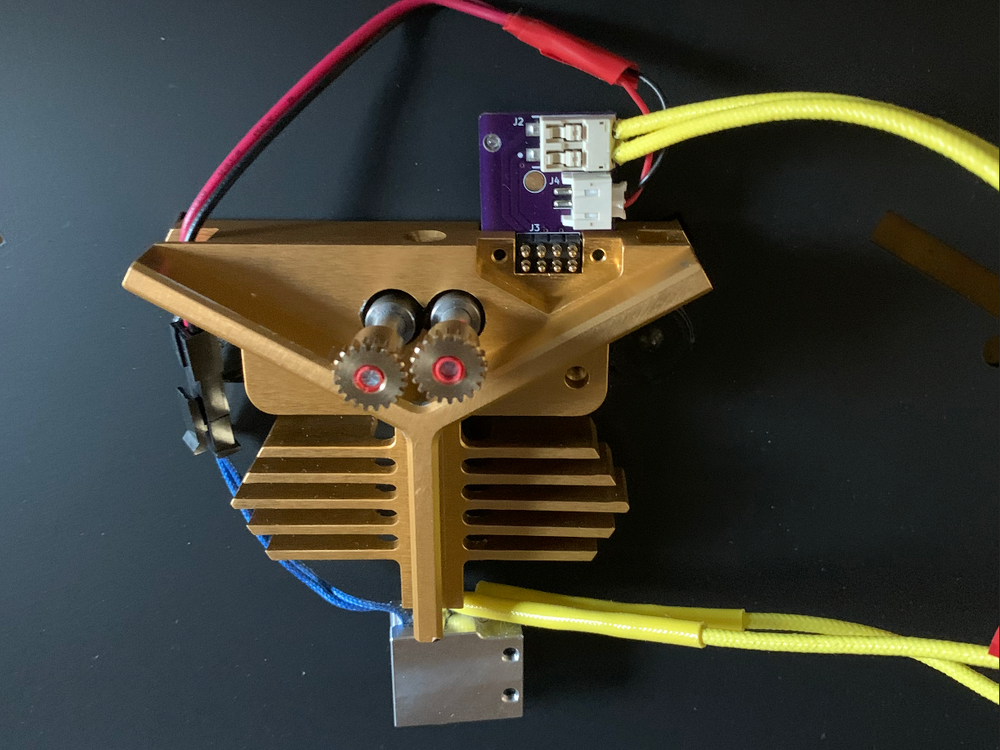
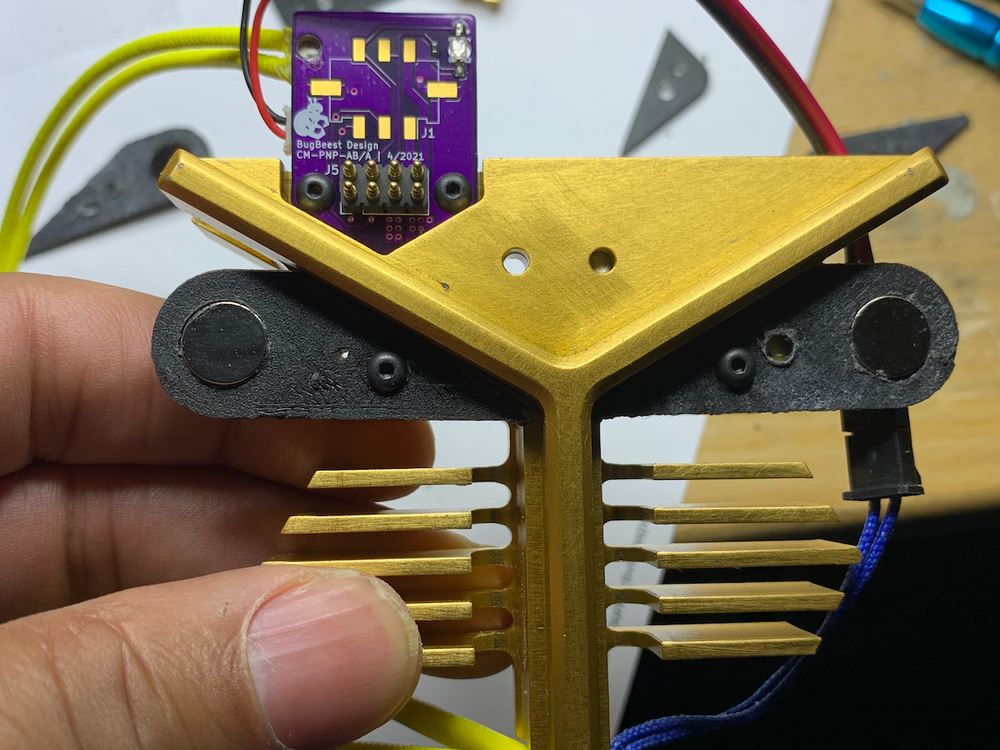
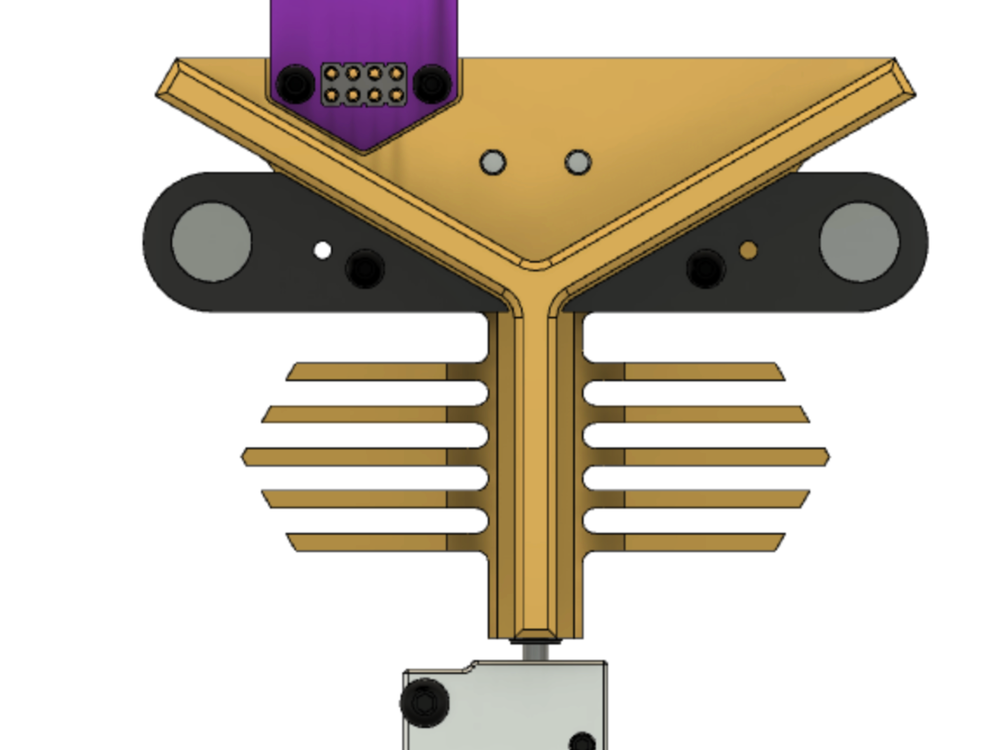
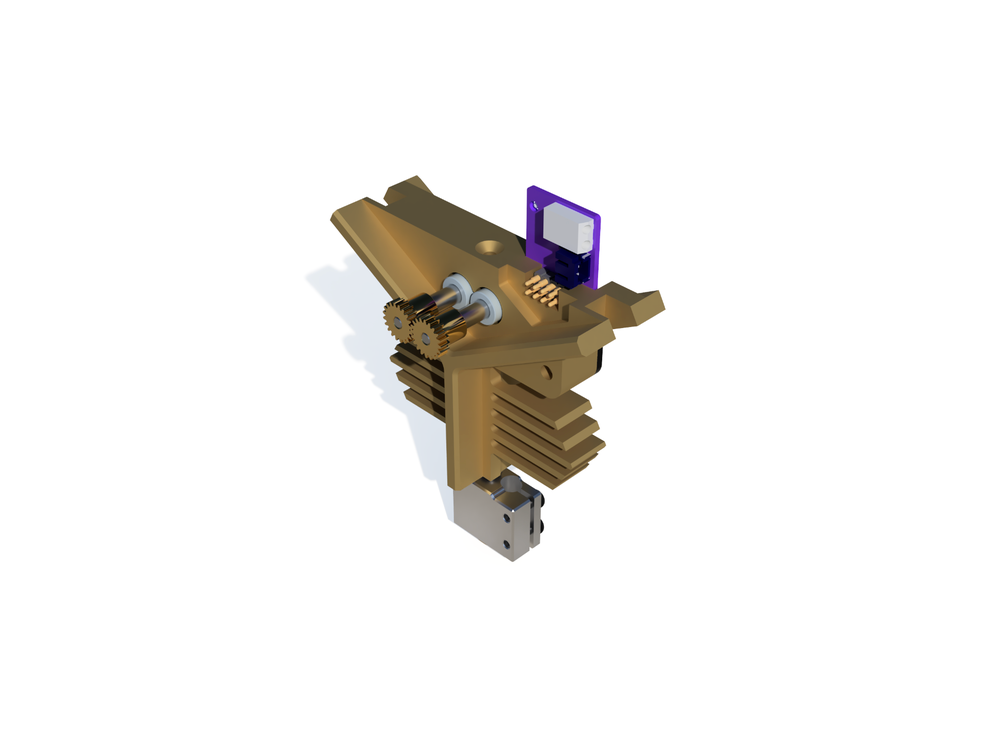
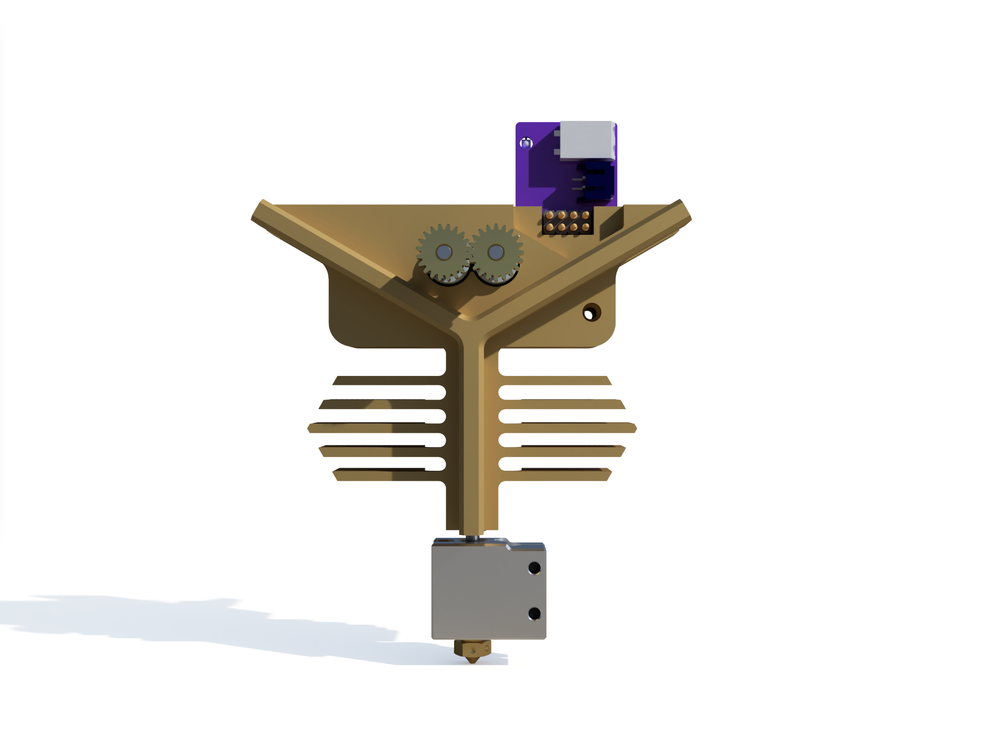
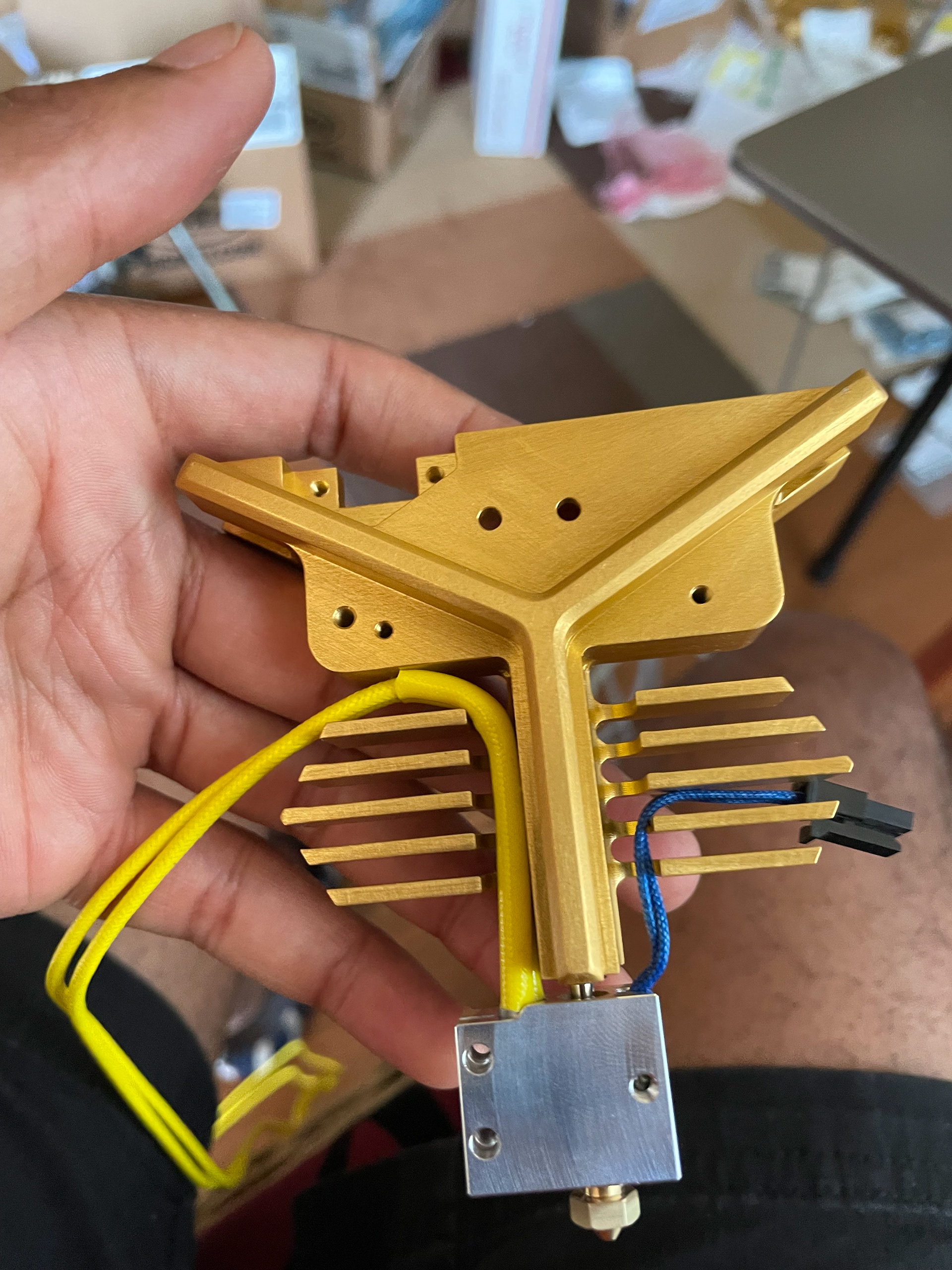