Folding robotic arm for aircraft assembly
2023 | Client: Airbus Robotics | Role: Mechanical Engineer
Project overview
To support Airbus’s drive to speed up production amid a backlog of aircraft orders, I designed a pneumatically powered robotic arm to automate the manual drilling of test holes and installation of fasteners. Built with a 4-bar linkage system, the arm folds compactly into a narrow space between the aircraft and surrounding equipment, then extends precisely to align with a second robot performing drilling operations.
Key contributions included:
• Space-Efficient Folding Mechanism: Engineered the 4-bar linkage to allow the arm to fold and extend within a tight space, maximizing reach while maintaining a compact footprint.
• Pneumaticaly Operated: Leveraged pneumatic power for reliable, repeatable movements essential to high-speed production and alignment.
• Rigorous Simulation and Testing: Conducted simulations and built scale models to ensure the arm operated within predictable ranges of motion, avoiding the instability that can occur with certain 4-bar linkage configurations.
• Pneumaticaly Operated: Leveraged pneumatic power for reliable, repeatable movements essential to high-speed production and alignment.
• Rigorous Simulation and Testing: Conducted simulations and built scale models to ensure the arm operated within predictable ranges of motion, avoiding the instability that can occur with certain 4-bar linkage configurations.
This project required extensive study of 4-bar linkages to manage their sometimes unpredictable behavior, and I refined the design to ensure consistent, stable operation. My role as product design engineer included end-to-end design, simulation, and validation, resulting in a robotic solution that effectively streamlined Airbus’s drilling process and enhanced production efficiency.
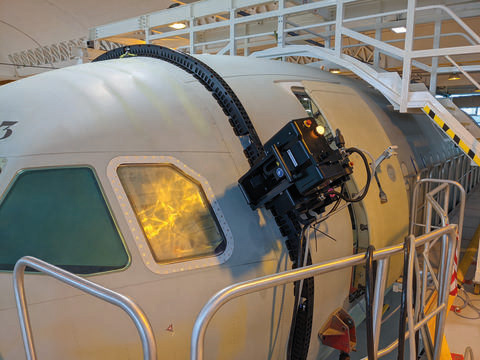