Multi-Material 3D PRINTER
Revolutionizing How Electronics Are Made
2021 | Client: Electronic Alchemy
The Multi-Material 3D Printer project was a continuation and transformation of an earlier design, which I took over to address fundamental challenges and unlock new capabilities. This 3D printer was designed to empower educators, researchers, and hobbyists by enabling the seamless printing of complex electronics within a single build process. By integrating multiple materials, each with distinct electronic properties, users could create fully functional electronic devices directly from their 3D printer. My role involved overcoming significant technical hurdles, implementing a novel approach to multi-material printing, and bringing a vision of accessible, DIY electronics to life.
Concept Overview
The primary goal was to create a 3D printer that could seamlessly print electronic devices by switching between specialized materials. The printer was designed to print electronic circuits and components alongside structural elements, enabling users to create a wide range of products in fields like education, research, and rapid prototyping. This includes the ability to print custom sensors, functional prototypes, and more—directly within a single build process.
An example of its potential is the creation of a touch-sensitive smart lamp:
• Building the Core Structure: The printer uses a structural filament to build the lamp’s body, including cavities for electronic components.
• Printing the Electronics: A conductive filament is used to print the wiring and contact points, while specialized capacitive filaments create a 3D-printed touch sensor embedded directly into a region of the lamp’s surface. This enables users to activate the lamp with a gentle tap, without the need for additional wiring or sensors.
• Plug-and-Play Assembly: Users can simply place a battery into a designated slot at the bottom of the lamp, where it connects to the printed circuits. An LED placed at the top makes contact with pre-printed connections, creating a working circuit. The result is a sleek, touch-activated smart lamp that lights up instantly with a touch, all printed in a single build process.
This example showcases the printer’s ability to handle multiple materials and create integrated electronic products, but the potential applications extend far beyond this use case.
Design Strategy: Balancing Innovation and Market Needs
From initial concept to pre-production, the project evolved to meet both technical and market-driven requirements:
• Differentiated Design: I designed the printer's exterior to stand out through anodized color options and a distinctive hexagonal prism shape, offering aesthetic appeal across different models. This allowed customers to select a model based on their budget and desired look, while maintaining consistent internal functionality.
• Custom Extruder Solution: Addressing a critical spark and fire hazard issue in off-the-shelf extruders, I commissioned a custom PCB with spring-loaded pins, ensuring safe and consistent contact with the printer’s extruders. This solution not only improved safety but also enhanced the reliability of material switching during operation.
• Adaptable Pricing Model: Developed different models for various price points, ensuring that features scaled appropriately with cost. This made the printer competitive with both Ultimaker S5 at the high end and Ultimaker S3 in a more compact, cost-effective offering.
Purpose: Expanding the Horizons of 3D-Printed Electronics
The Multi-Material 3D Printer was developed specifically to enable the creation of complex, functional electronics through additive manufacturing. It targeted educational institutions, research labs, and advanced hobbyists, allowing them to prototype custom electronic devices quickly and affordably. The printer’s ability to integrate structural and electronic elements in a single build makes it ideal for applications ranging from educational models to innovative prototypes that require more than just plastic parts.
Iterative Development & Prototyping
Taking this project from concept to pre-production involved multiple iterations, each aimed at refining the design and validating its capabilities:
• Prototyping for Validation: Developed two pre-production candidates that were fully sourced and assembled for validation testing. These prototypes served as proof of assembly and underwent rigorous testing for shipping survivability and integration of the pick-and-place mechanism.
• Testing & Feedback Loop: Through hands-on testing, we identified improvements in material handling and assembly processes, leading to adjustments in extruder alignment and calibration. These refinements ensured that the printer maintained precision even when switching between materials.
Results & Strategic Pivot
As the project progressed, changing market needs and client feedback prompted a strategic shift in scope:
• Refining the Scope: Initially designed to compete with the Ultimaker S5, the printer’s focus shifted when the client decided to target the Ultimaker S3 market. The emphasis moved from large-scale, feature-rich builds to a compact, user-friendly design that maintained core multi-material capabilities.
• Downsizing for Market Fit: I adapted the printer’s frame and extruder arrangement to create a more compact version, reducing overall size while maintaining the ability to print complex electronics. This pivot allowed us to position the product as a versatile, affordable solution in the mid-market segment.
• Securing Manufacturing Partnerships: Identified and partnered with a manufacturer capable of scaling production, ensuring that we could meet demand while keeping costs competitive.
Key Innovations & Technical Leadership
• Internal Pick-and-Place Mechanism: The core innovation of the Multi-Material 3D Printer was the pick-and-place system for handling multiple extruders. This mechanism allowed the printer to automatically switch between different materials during a print cycle, maintaining precise temperature control and preventing filament cross-contamination.
• Custom Safety Solutions: To resolve the fire hazard issue of earlier extruder designs, I commissioned a custom PCB with spring-loaded pins, ensuring safe and reliable electrical contact for each extruder. This approach enhanced overall safety and reliability, reducing the risk of overheating during prolonged use.
• Strategic Adaptation for Market Needs: My ability to quickly adapt the design to meet evolving client requirements ensured that the final product remained competitive in the mid-market segment, balancing affordability with advanced multi-material capabilities.
Impact
• Enabling New Possibilities in Education and Research: The printer’s ability to seamlessly integrate multiple materials allowed educators and researchers to prototype electronics quickly. It enabled hands-on learning and experimentation with advanced materials, making it possible to create everything from touch-sensitive smart lamps to custom sensor arrays directly from a classroom or lab.
• Cost-Efficient Manufacturing Strategy: Clever use of part consolidation allowed the printer to be produced at a competitive price while maintaining flexibility during production, ensuring that we could adapt to changing market conditions without sacrificing quality.
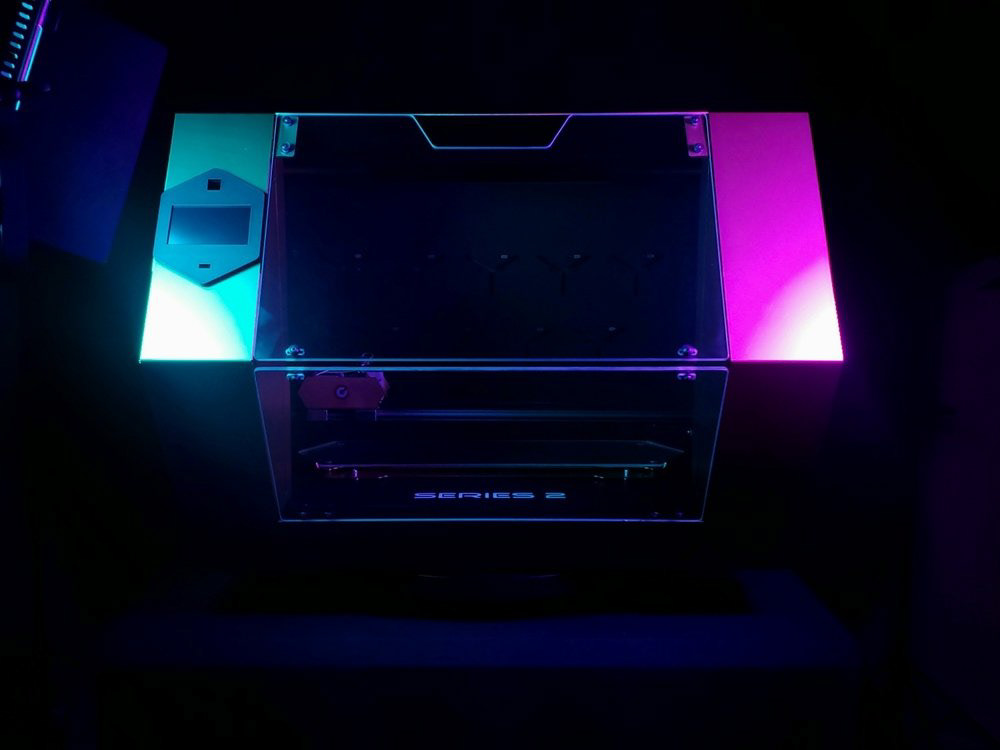
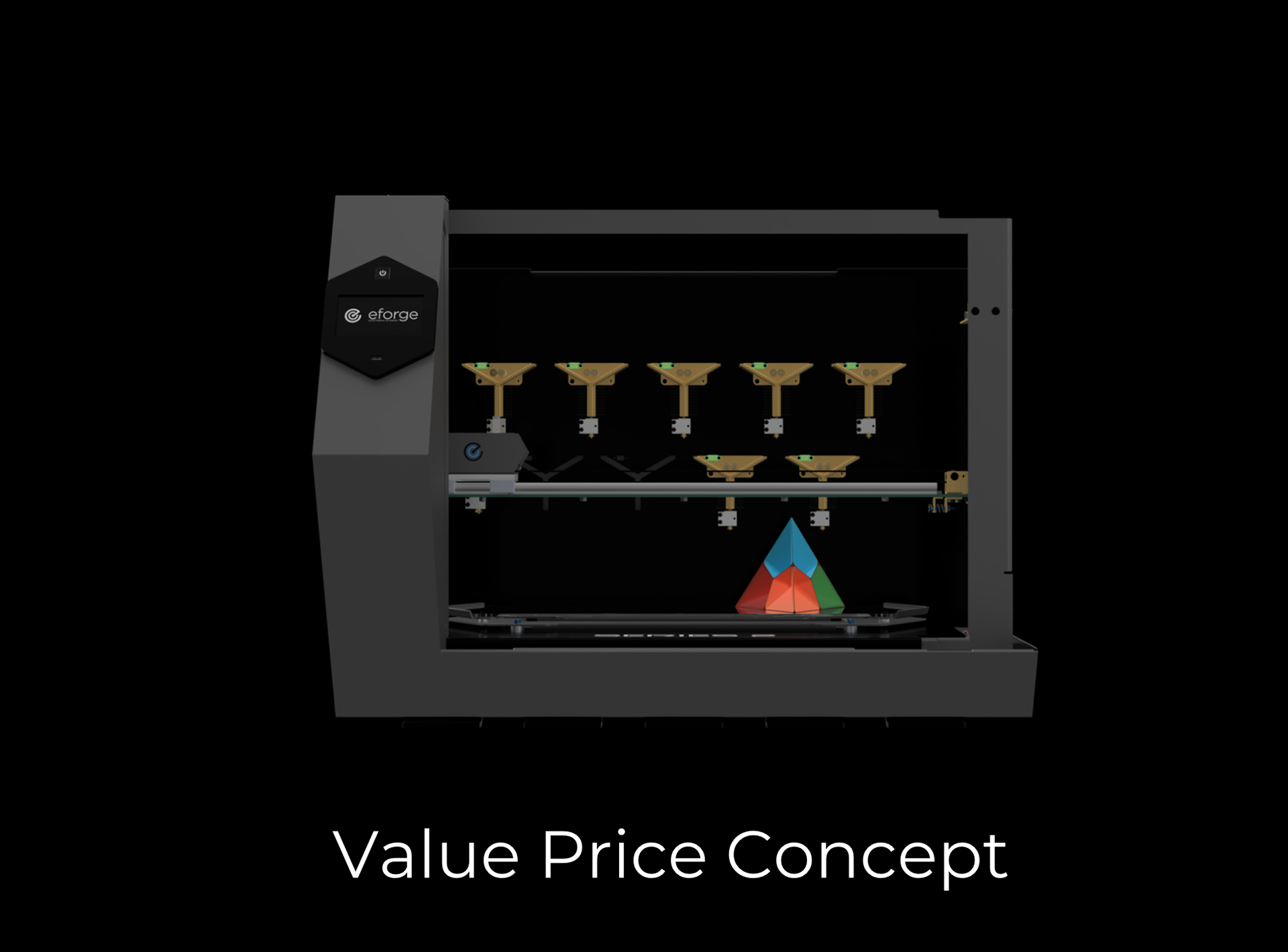
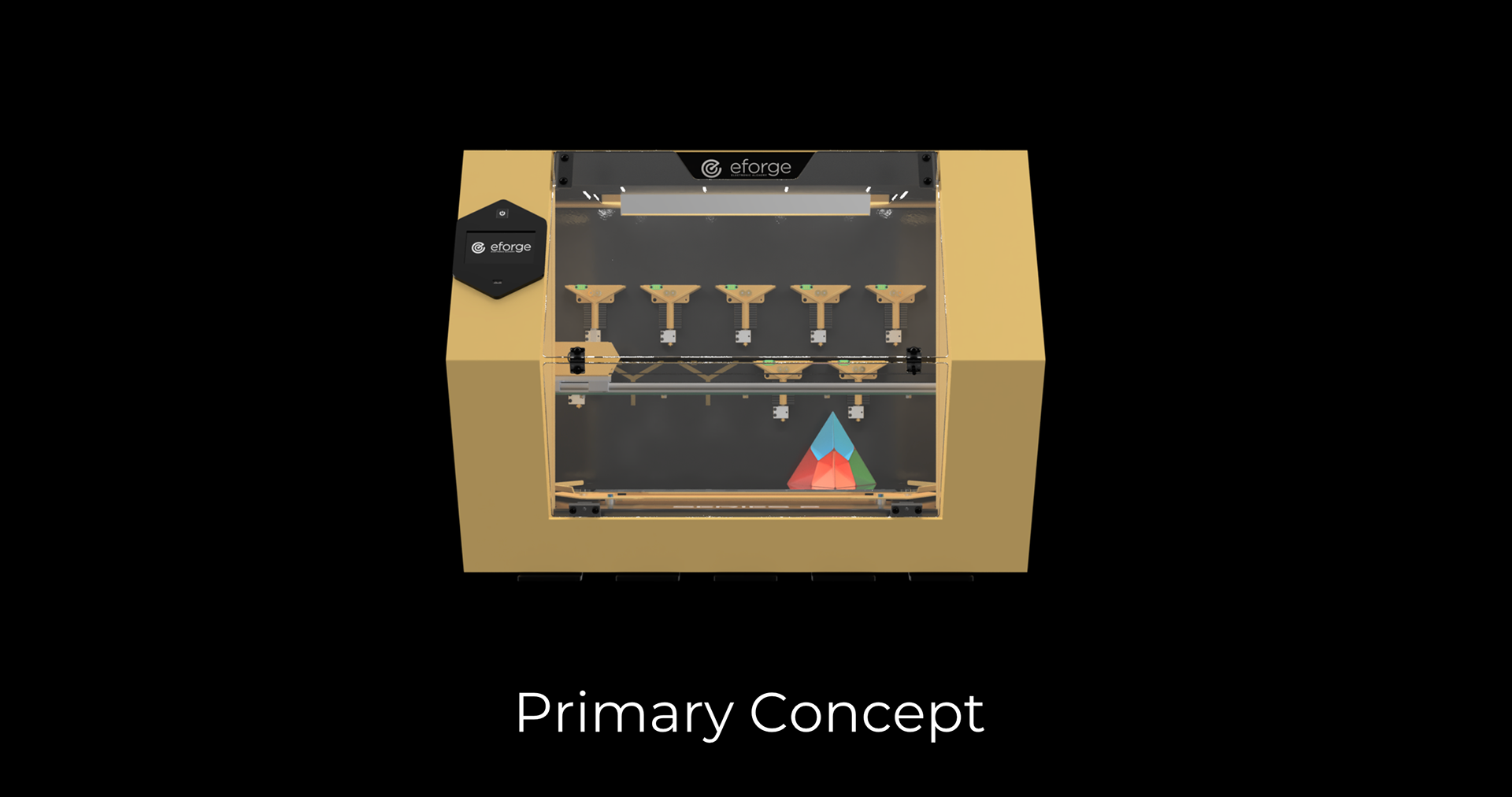
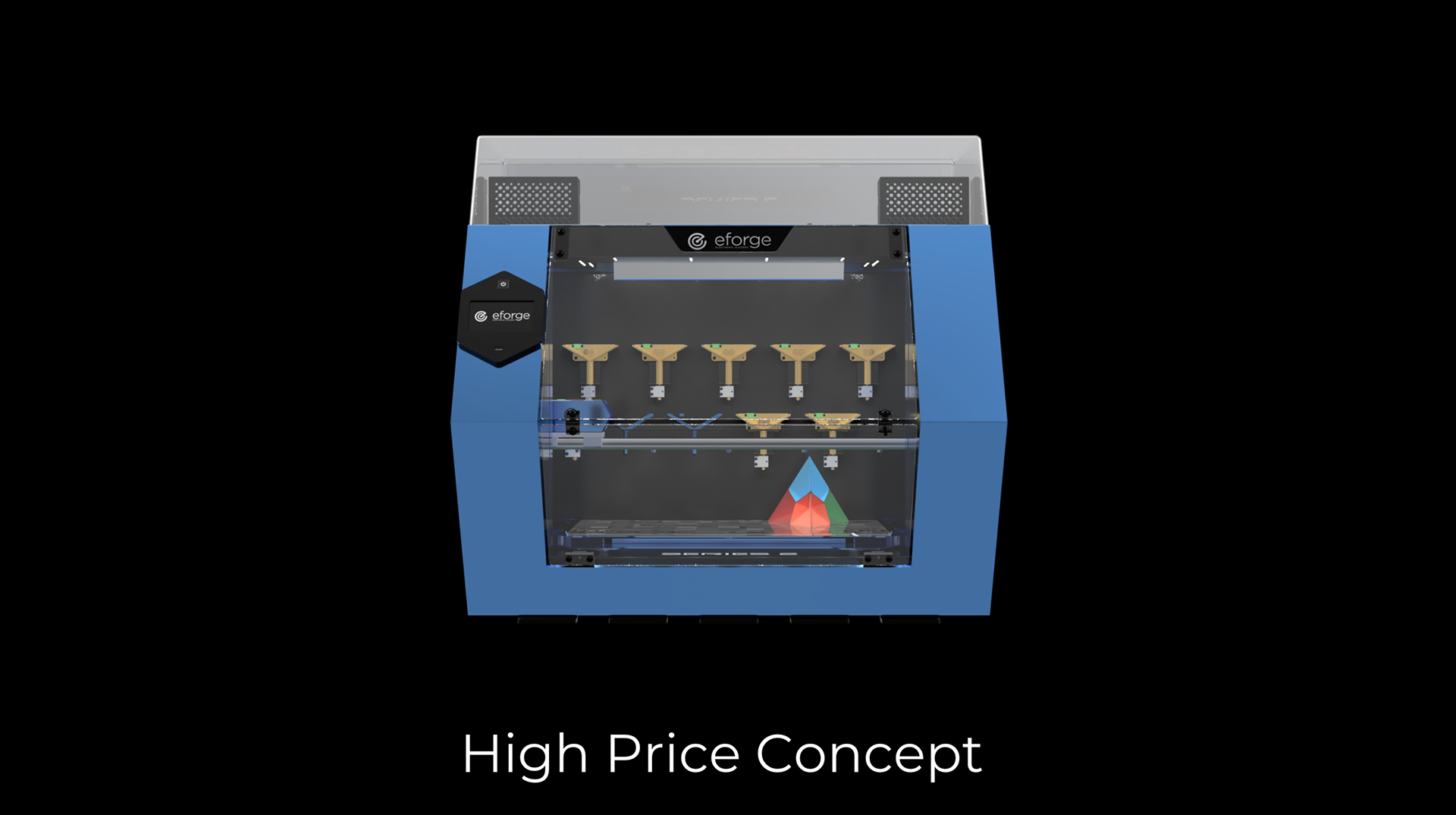
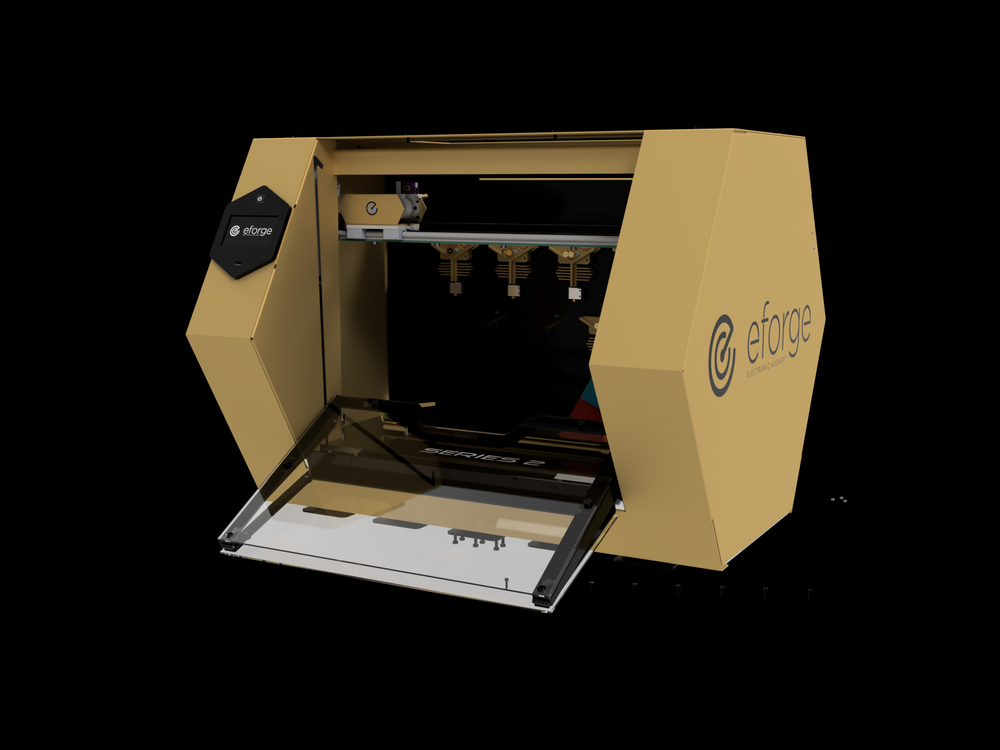
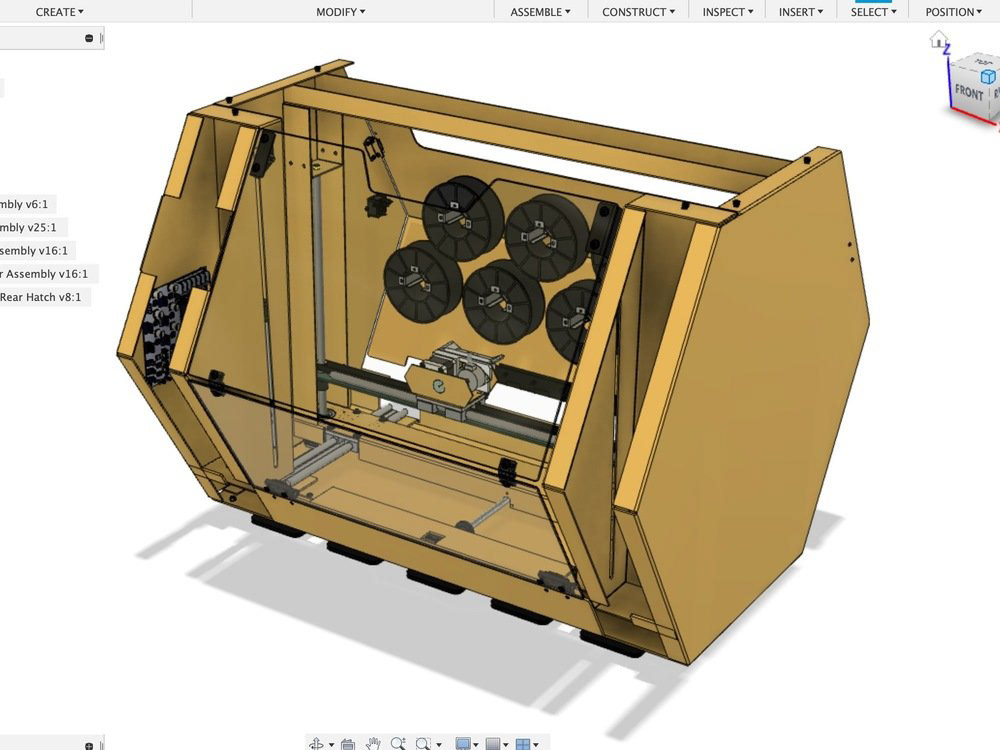
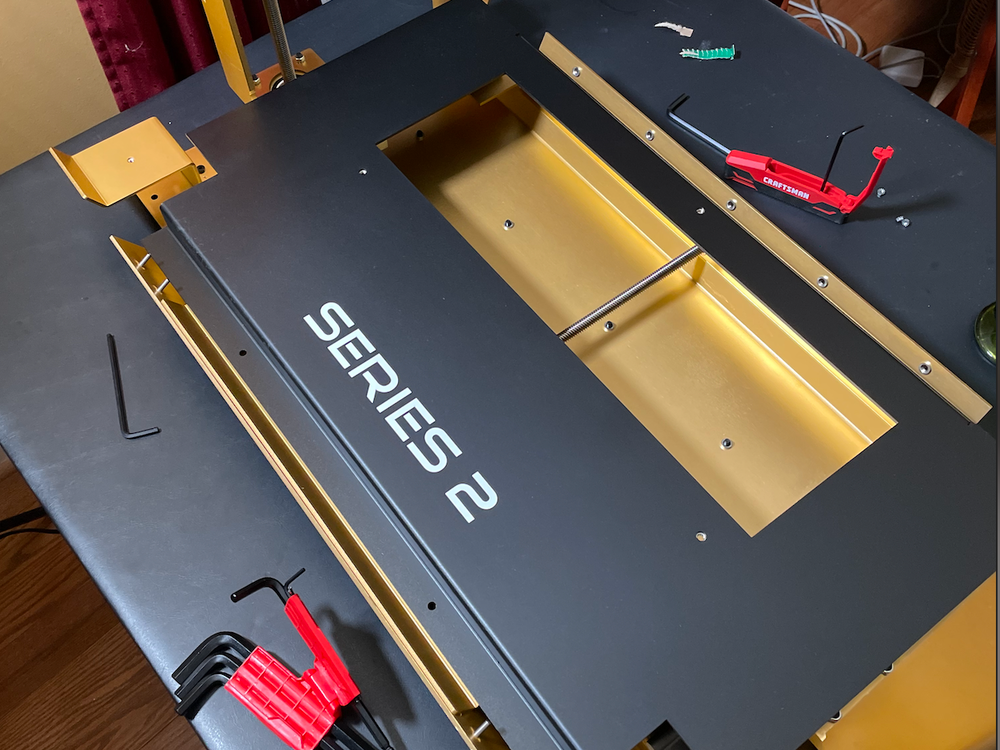
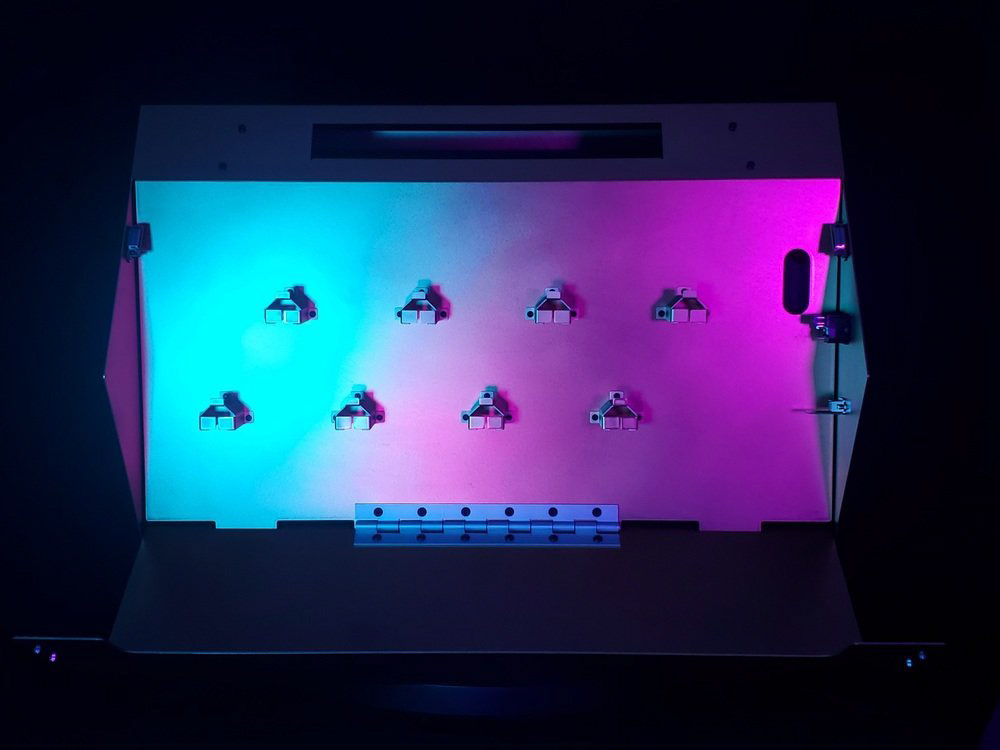
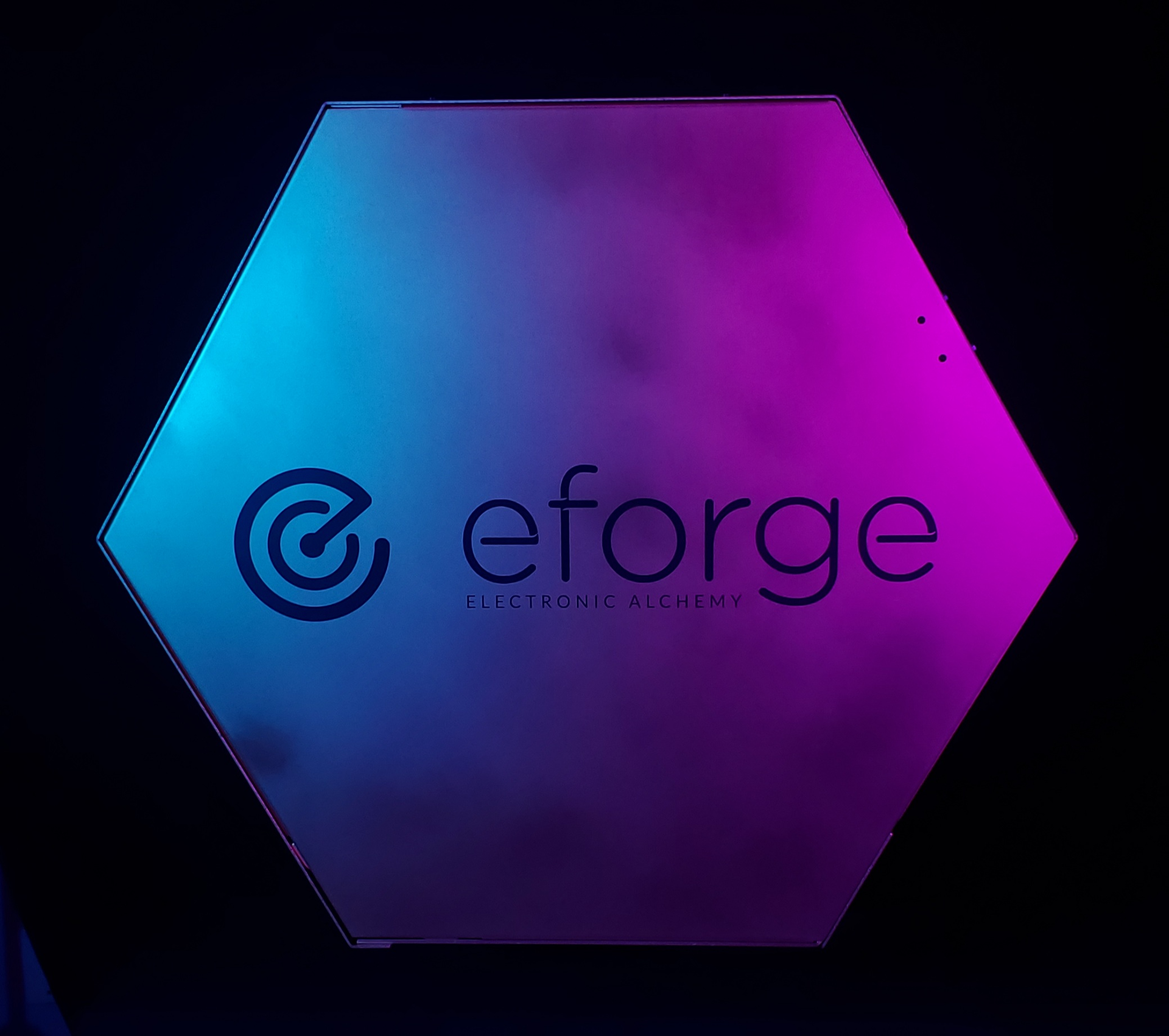
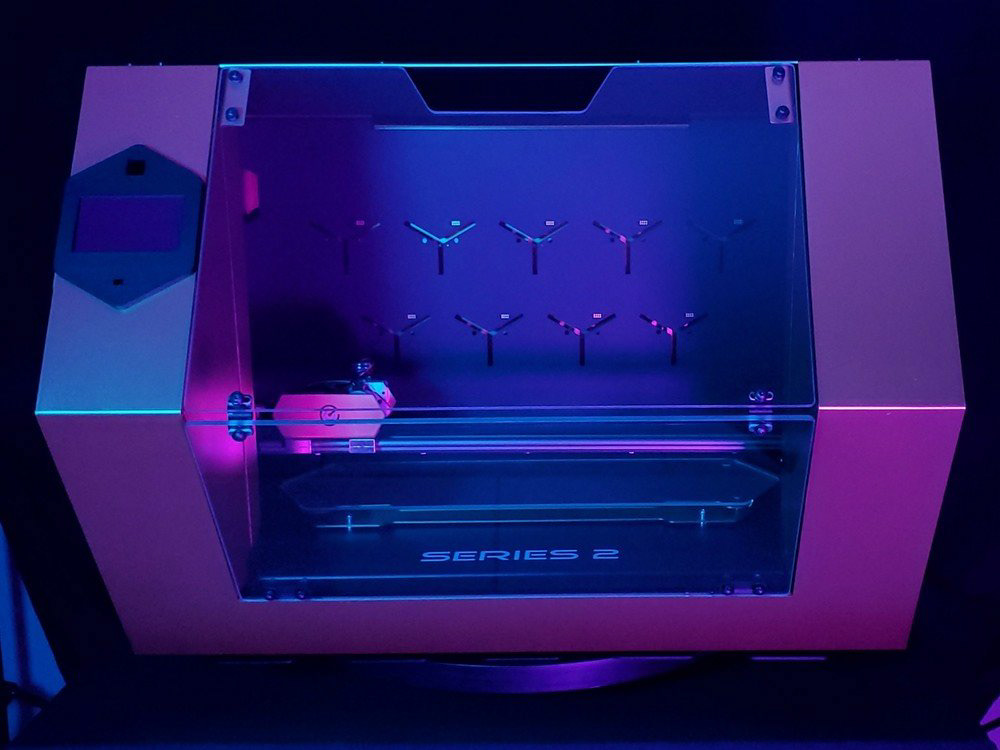
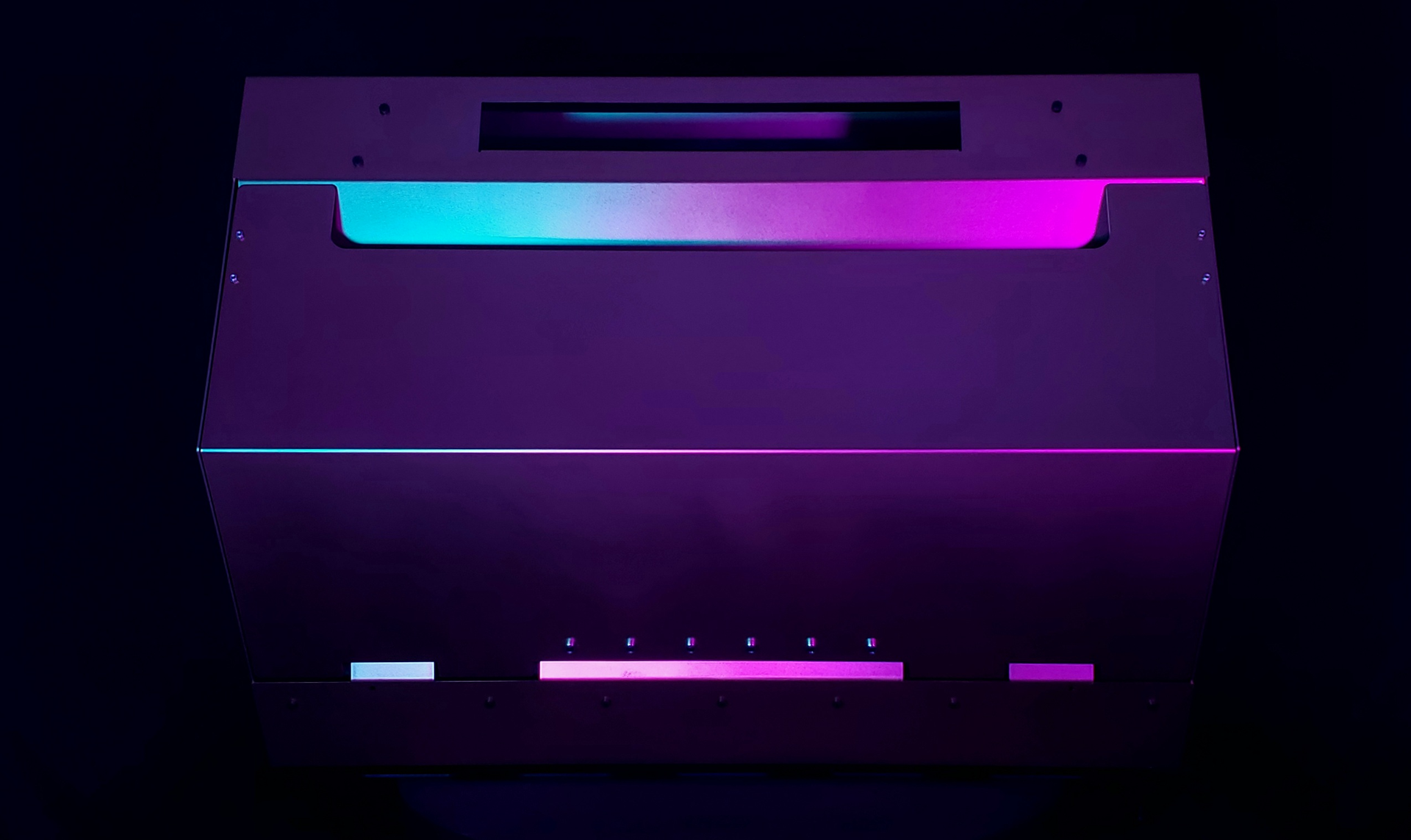
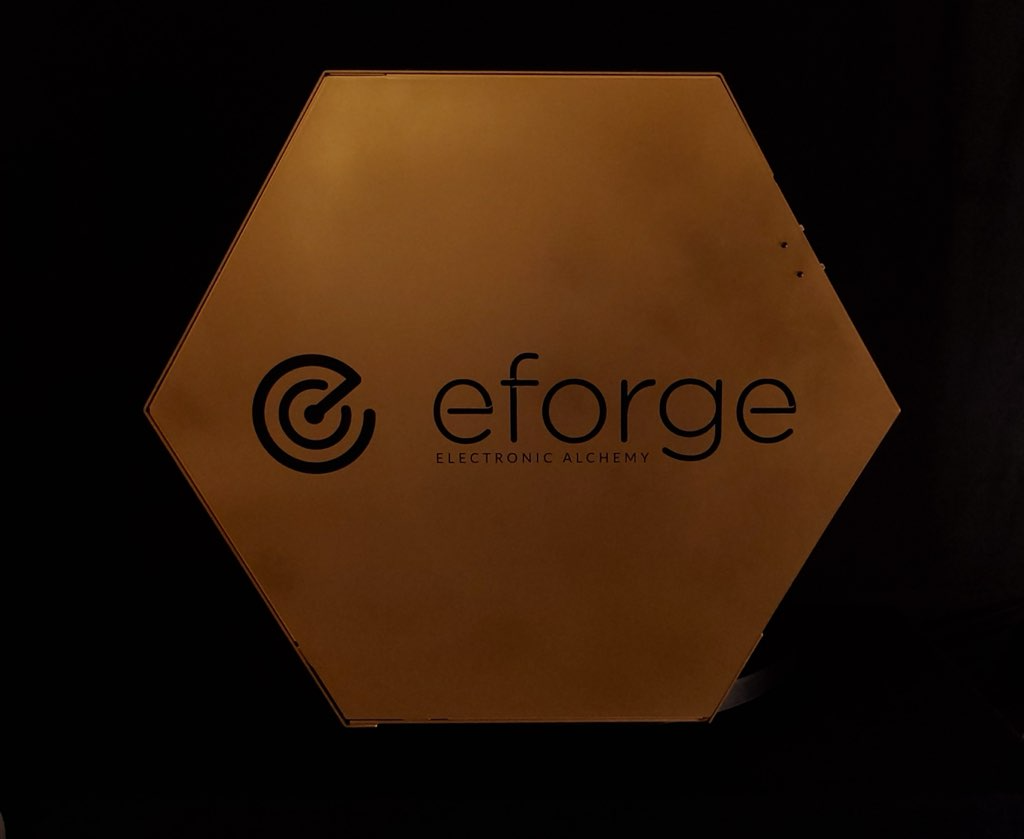
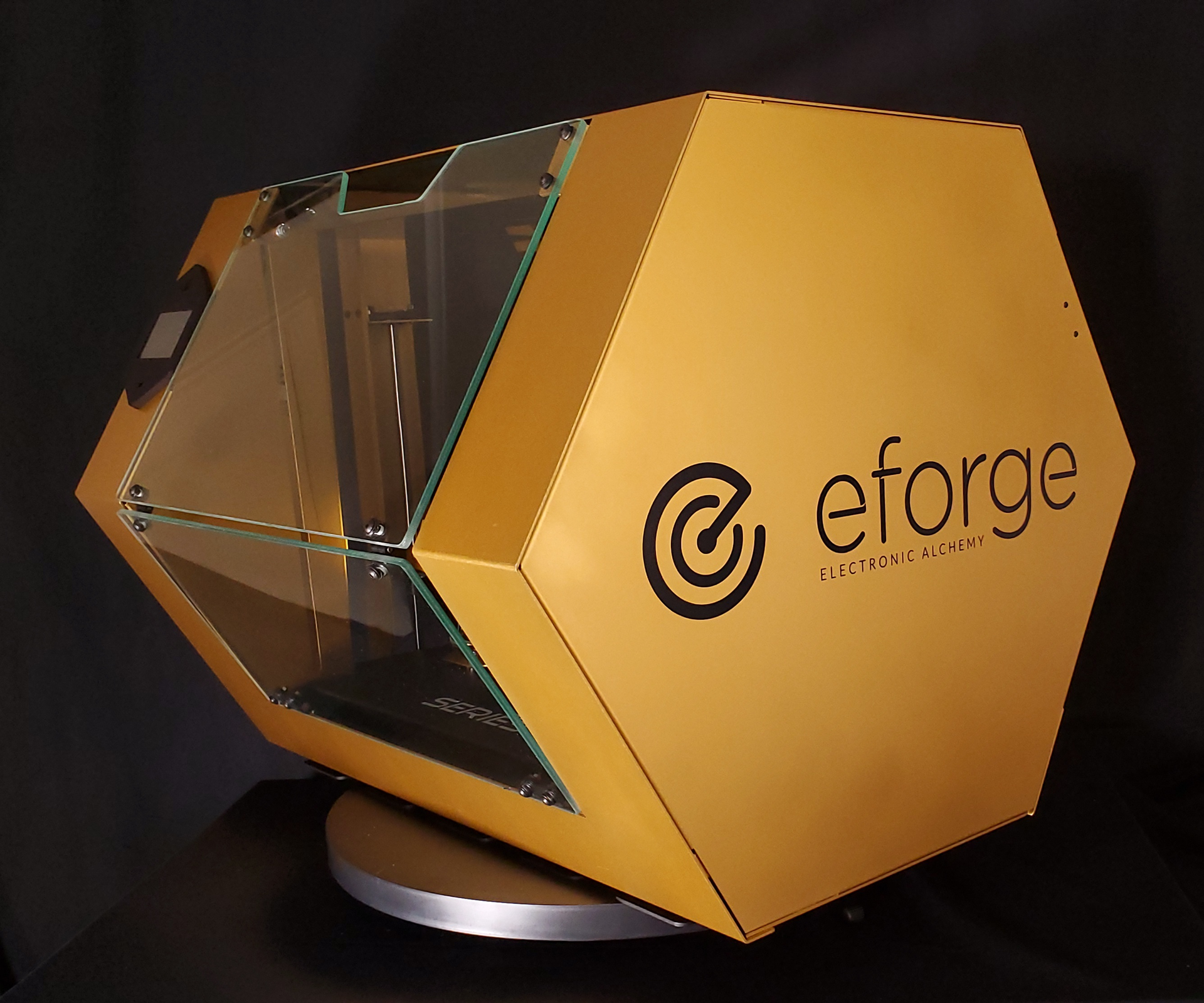
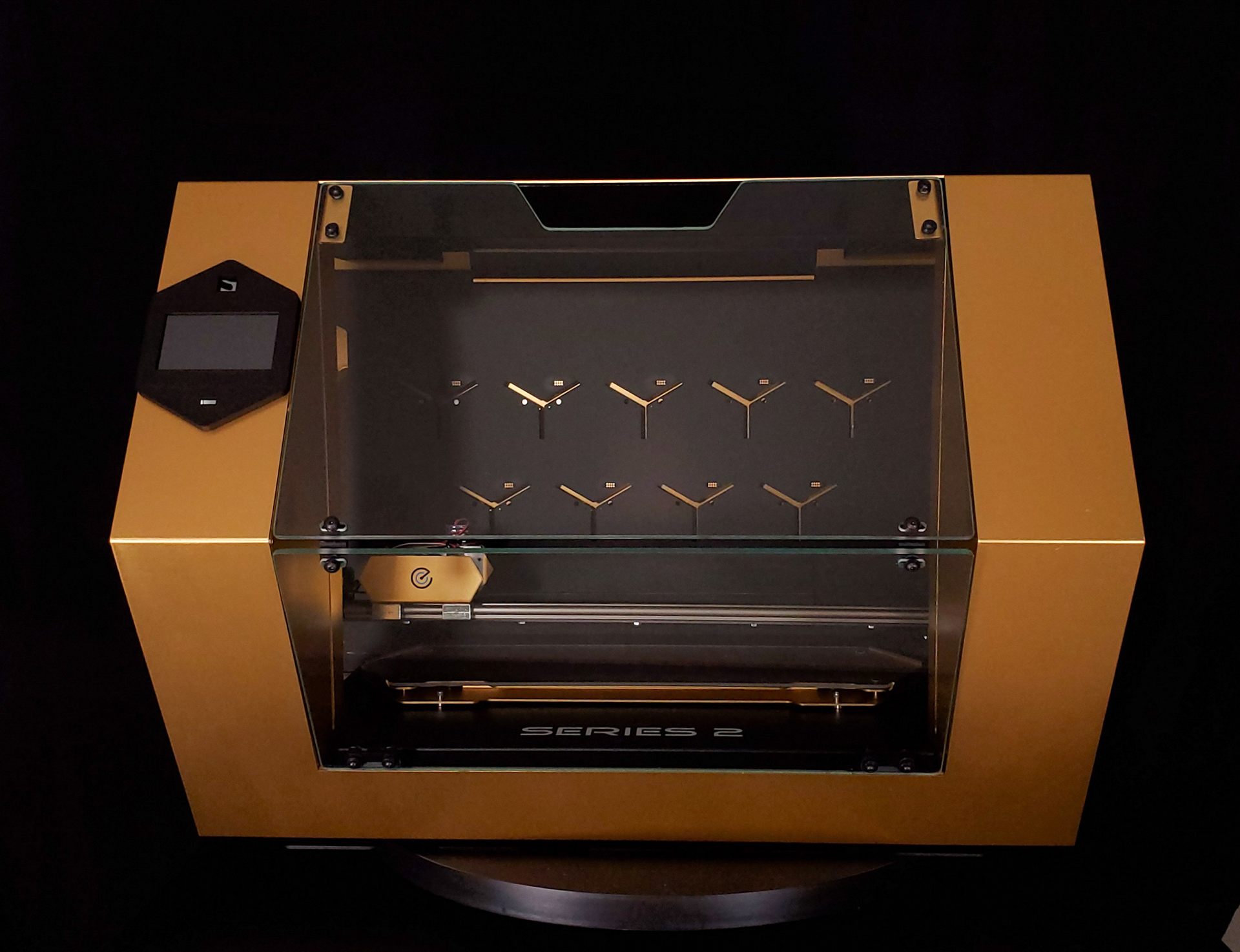